The belief that all radar level gauges are unsuitable for providing accurate and reliable measurements in liquefied gas tanks is quite simply untrue, explains Christoffer Hoffmann, business development manager for liquefied gases at Emerson
Within the tank storage industry there is a common misconception that radar is not a suitable technology for providing accurate and reliable level measurements of liquefied natural gas (LNG), liquefied petroleum gas (LPG) and other natural gas liquids, such as ethane.
However, this is categorically untrue. Modern non-contacting radar devices can actually excel in measuring the level of these liquefied gases, which is proved by the fact that they are already being successfully used on more than 10,000 LNG and LPG tanks globally.
The fallacy about radar’s supposed unsuitability for use in liquefied gas applications originated due to concerns that a combination of vapour in the tank and weak signal reflection could impact the performance of instruments based on this technology. It is this belief which has led some organisations to continue using inferior servo gauges to provide level measurements in liquefied gas tanks, despite the various disadvantages of this older and less reliable technology.
There is no dispute that liquefied gases often produce vapours in a tank, and that these vapours can affect the propagation speed of radar waves. This can then impact the measurement accuracy of some radar level gauges. Furthermore, variations in temperature and pressure cause changes in vapour saturation degree, which can also affect radar signal behaviour and measurement accuracy. It is also true that liquefied gases typically have a much lower dielectric constant than water or oil, for example, and that this results in weaker radar signal reflections, making it more difficult for some radar level gauges to distinguish the level signal from background noise.
However, these facts alone do not tell the whole story, because modern, well-engineered non-contacting radar devices – such as the Rosemount 5900S Radar Level Gauge from Emerson – can overcome these issues and maintain excellent measurement accuracy and reliability. In fact, during four decades of service on LNG and LPG tanks, no Emerson radar installation has experienced any accuracy- or reliability- related problems due to the presence of vapour, which perfectly illustrates the suitability of this technology for use on liquefied gas tanks.
Vapour Compensation
Non-contacting radar level gauges can compensate for the presence of vapour in liquefied gas tanks – and the effect of the vapour on the radar waves – by utilising an integrated pressure transmitter. This sensor measures the vapour pressure inside the tank, and the gauge can then calculate the influence of vapour on the microwave propagation speed by combining the pressure measurement with information about the liquefied gas type and mixture. Compensating for the effect of vapour in this way enables level readings to be automatically corrected, ensuring excellent measurement accuracy of +/-0.5 millimetres, in the case of the Rosemount 5900S. An integrated pressure sensor also helps to determine the vapour saturation degree. This data then enables the tank gauging system to dynamically compensate for variations in signal speed caused by changing tank conditions, thereby maintaining measurement accuracy.
Real-Time Corrections
Combining level and pressure measurement into a single device simplifies installation and system architecture, streamlines maintenance and reduces costs. It also enables real- time measurement corrections, whereas having separate devices can introduce small delays in data processing, affecting real-time performance. As conditions inside a tank change – due to filling, emptying, or temperature fluctuations, for example – the tank gauging system continuously updates its calculations to ensure consistent measurement accuracy. These real-time corrections are critical from a safety viewpoint. LNG and LPG are hazardous fuels, so precise and dependable level measurements are essential in helping to prevent spills and leaks that could pose severe risks to personnel, including fire, explosion and asphyxiation
Overcoming Weak Signal Reflections
To overcome the problem of liquefied gases having a low dielectric constant, the latest non-contacting radar level gauges leverage frequency modulated continuous wave (FMCW) technology, with a sensitivity more than 30 times greater than devices using older pulse modulation techniques. This heightened sensitivity maximises signal strength and enables FMCW devices to deliver superior measurement accuracy and reliability. A wide dynamic range enables these devices to detect both strong and weak radar signal reflections effectively and process them reliably. Superior signal processing algorithms enable noise to be suppressed and filtered, enhancing the detection of weak echoes and producing a more robust and reliable measurement.
To further enhance their performance, non-contacting radar level gauges use antennas designed specially to optimise measurement accuracy and address the challenges posed by liquefied gas applications. These robust antennas are designed to ensure optimal transmission and reception of radar signals, even when the dielectric constant is low, and to withstand low temperatures, enabling them to operate effectively in cryogenic conditions. It is also recommended that radar signals should be guided within a still-pipe, as this reduces signal dispersion and helps to amplify the radar echo from the surface of the liquefied gas, further optimising signal strength and measurement accuracy.
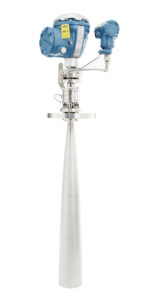
Radar Advantages Over Servo
If tank storage organisations accept that well-engineered radar level gauges provide excellent accuracy and reliability in liquefied gas level measurement applications, they should then consider the benefits they can achieve by selecting this more modern technology rather than servo gauges. Although still widely deployed on LNG and LPG tanks, servo gauges are complicated devices with numerous moving parts, which renders them susceptible to mechanical wear. As a result, the mean time between failures (MTBF) of servo gauges can be as little as five years. Maintenance and calibration are often regularly required to keep devices in good condition – which leads to increased safety risks through workers making more trips to the field – and a large stock of spare parts is required.
A servo gauge can be isolated from chamber above the ball valve enabling technicians to gain access. However, because it is difficult to determine if the displacer is fully wound up above the ball valve, the wire can sometimes break when closing the valve. When this happens, the displacer and the wire will fall to the bottom of the tank. Not only must a new displacer and wire be fitted and calibrated after each breakage, but the broken parts could cause serious problems if they were sucked into pumps and valves.
Impact Of Liquid Density Changes
Another issue for servo gauges is that their measurement accuracy can be significantly affected by changes in liquid density. This is because the buoyant force acting on the displacer changes with the density of the liquefied gas. If the density decreases, the displacer experiences less buoyant force, and the gauge may interpret this as a lower liquid level than is actually the case. Conversely, an increase in density could be misinterpreted as a higher level. A servo- based tank gauging system therefore needs to compensate for liquid density changes to avoid level measurement errors which could lead to increased safety risks, inaccurate inventory records and custody transfer disputes.
Reliability Is Crucial
Level measurement devices with excellent reliability are vital in liquefied gas applications, as this not only helps to increase safety but also optimises the operational availability of tanks. This is a critical requirement because tank downtime can result in financial losses, can impact demand fulfilment and disrupt supply chains, and can affect inventory management.
In stark contrast to servo gauges, non- contacting radar level gauges deliver outstanding reliability, even in the most challenging applications, with an MTBF for critical parts measured in decades.
Because these instruments are non-contacting there are no wetted parts, and combined with a lack of moving parts, this minimises their maintenance requirements. Non-contacting radar level gauges used in liquefied gas applications will therefore have a very long service life, and can easily operate for 20 years without any need for maintenance or adjustment, which helps to reduce their total cost of ownership. The design of these devices enables their availability to usually reach close to 100% during their long lifespan. In the unlikely event of a non-contacting radar level gauge suffering a failure, diagnostic software will typically identify it and take the device to a safe state.
Online Verification Without Interrupting Operations
Among the integrated diagnostic tools enabling the Rosemount 5900S to achieve enhanced reliability is online verification capability, which allows users to continuously or periodically monitor and verify a device’s performance without interrupting operations. A reference pin provides a fixed, known reflection point for the radar signal. By comparing the measured signal with the known characteristics of the reference pin, the tank gauging system can detect any issues – such as signal degradation, hardware malfunctions or calibration drift, for example – that could potentially affect measurement accuracy and reliability. Because the verification is performed without interrupting operations or requiring physical intervention, this increases safety and operational efficiency. Early detection of any potential issues prevents unexpected failures and allows for pre-emptive maintenance, reducing downtime and costs.
Conclusion
Because well-engineered non-contacting radar level gauges can compensate for the effects of vapour, this creates the opportunity to successfully implement these devices in liquefied gas level measurement applications and gain the benefits they provide over older and less sophisticated servo technology.
Greater reliability, minimal maintenance, and lower start-up and lifecycle costs combine to ensure safe, reliable and efficient operations, with minimised downtime and costs.