Dearman Systems has been providing innovative software solutions to the refined petroleum industry for over three decades. The company’s solutions are primarily used in the storage and transportation segments of this industry.
Dearman System’s Terminal Automation System (TAS.net) is used on over 200 storage terminals worldwide. It combines the Internet of Things (IoT) with process control capabilities to automate operations and reduce manual processes to ultimately bring cost savings and operational efficiencies to its users.
Dearman’s TAS is able to push and pull data at a given site across hardware and software in order to prompt carriers to complete operational tasks without the need for heavy labour. The TAS is able to talk to weight scales, loading arms, security gates, tank inventory gauges, printers and much more so that
terminal operators can automate daily tasks and reduce repeat work and manual processes.
Terminal automation separates itself from traditional programmable logic controller (PLC) or Supervisory Control and Data Acquisition (SCADA) solutions in its ability to push and pull data, rather than to pull data alone from siloed devices. This ability to integrate all of this into one platform gives operators the eyes on their operations from anywhere, it allows them to set business rules within the software’s logic for more efficient supply chain management and it gives them a foundation of infinite data points that can help operators grow intelligently, while offering better experiences for their customers, carriers and employees.
Dearman’s TAS can integrate with mostly any field device or software system in the industry, as they have continued to build integrations for over thirty years to ensure their sizable customer base is covered no matter what hardware or software they want to use outside of Dearman Systems.
Terminal automation sets up a company for digital transformation in the bulk liquids industry, but it shouldn’t stop there. Dearman Systems’ LYNX platform utilises terminal automation to enable the entire supply chain.
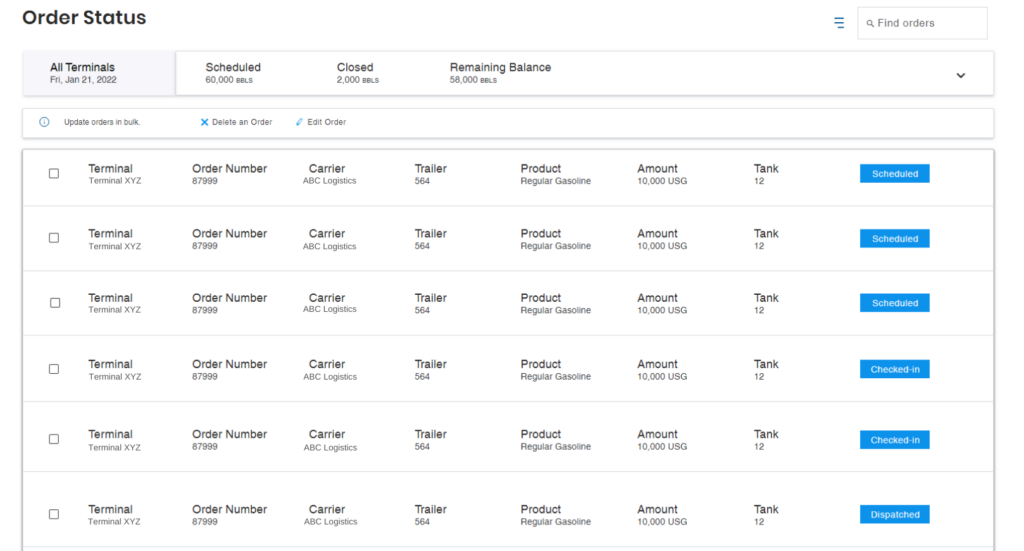
BEYOND TERMINAL AUTOMATION
Dearman Systems is launching a product called LYNX in 2022 which goes beyond terminal automation at the storage site and includes the entire supply chain. LYNX is a new way to coordinate and manage product movement tasks, and it benefits terminal operators, suppliers/position holders, customers and carriers. Just like Dearman’s TAS, LYNX can also be integrated into companies’ current hardware and software devices but LYNX alone is a cloud product requiring zero integrations for its core functionality.
LYNX was created to offer transparency into product movement without extensive labour or a chain of communication. The traditional industry standards for loading and transporting refined petroleum products have long been through allocations. Position holders would sell contracted volume to customers, and the customers would come pick it up and their allocations would adjust accordingly. At any given time, the position holder, terminal operator and customer do not have insight into what is happening with the product movement. There is no way for customers to know about supply issues or statuses without communicating with their position holder who may be doing business with a terminal operator, causing an even longer chain of communication to figure out what is happening with a pickup. LYNX changes all of this.
LYNX is a cloud platform that suppliers/position holders sign up for and input all their customers. Their customers input carriers, who can also access the platform. All product movement information such as allocations, credit, contracts, orders, pickups, product volumes, product pricing etc. is kept in LYNX for customers to quickly schedule pickups from suppliers in seconds. At that moment, LYNX authorises or rejects these pickups based on inventory, current contracts or allocations, credit or whatever the position holder or terminal operator wants to include in their rules prior to dispatching that customer’s carrier.
Once the order is approved by the position holder, the customer is prompted to dispatch their carrier within the timeframe the customer has allotted. The driver is then prompted through a series of authorisations and tasks based on their unique order number until the order is complete. Throughout this process, position holders, terminal operators, customers and carriers can see the status of that product movement in LYNX.
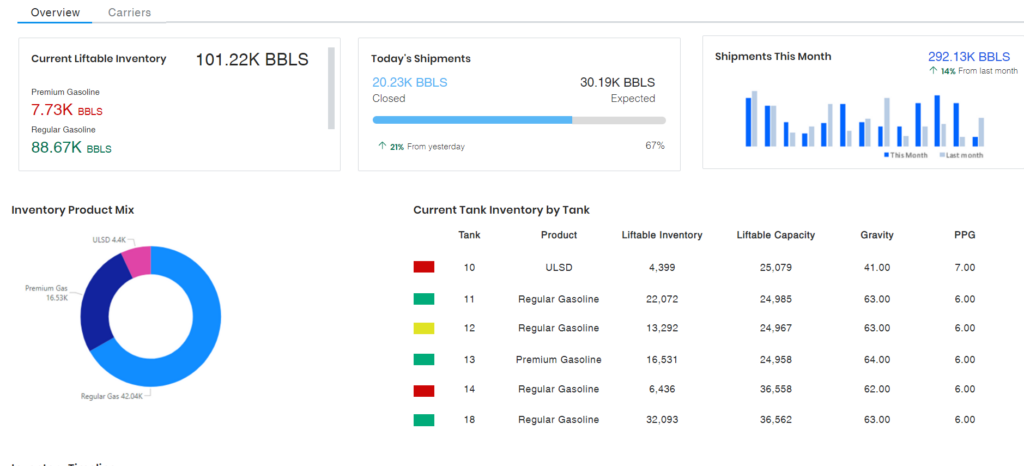
PRODUCT DEMONSTRATIONS
LYNX demonstrations are being offered by Dearman Systems throughout 2022. Its first customer, Bluewing Midstream, has been in a beta trial of LYNX for two years. Bluewing Midstream is a refined petroleum products storage terminal in Brownsville, Texas, US, and has been working with Dearman for almost four years. The company leases out storage space in its tanks and operates its terminals, providing value added services and software solutions to their customers to ensure quality and ease of use. Dearman conducted a customer survey with Bluewing this past year to get their thoughts on LYNX.
Bluewing’s head of automation and digital transformation Will Reid says that Dearman provides solutions to Bluewing for inventory management, custody transfer, access control and scheduling, order management and traffic control for truck, rail and marine product movements.
‘Since 2019, when Bluewing completed an implementation of LYNX for truck and rail with Dearman, corporate office labour as a percentage of EBITDA fell 77% and field labour fell 70%,’ says Reid. ‘We were able to utilise our software to put our labour to work in more useful ways. This allowed us to scale our operation while keeping headcount equal. We reduced error, eliminated redundancies, provided a better experience for our customers, and created transparency for our customers’ customers to run a more efficient business which ultimately helps us too. LYNX has been a game changer for us in this digital transformation.’
UNITY
On top of TAS and LYNX, Dearman Systems provides solutions for companies with multiple terminals, combining multi-terminal data into one platform for back office decision making and automated reporting. This product is called UNITY. UNITY serves as an umbrella of data and information for a company’s entire footprint. Companies can utilise this data to eliminate manual reporting and auditing, automate cross-functionality with enterprise resource planning (ERP) systems and accounting tasks, and gain insight into their supply chain from a higher level. UNITY can integrate with Power BI for companies looking to access dashboards or other business intelligence functionality. UNITY also allows companies with bigger footprints to make a change in one place at once and have it made at all of their sites, rather than repetitive work at each site.
Dearman Systems does a fair share of custom work that is requested of them for companies looking for unique solutions. They are staffed adequately to handle all sizes of requests pertaining to supply chain software needs for customers in the bulk commodities industry.
For more information: